How to save a robot from drowning with the use of a filter
A packaging company recently came to us with a problem to do with their air operated process picking arms. At their packaging plant due to limited space and complicated routing of compressed air lines – which are notoriously wet and dirty – water was swamping the filters and travelling straight to the robotic process picking arms.
It was not that air operated automation is a new technology but two other leading filter companies had failed to solve the problem and the downtime was impacting their business. We were delighted to be recommended as ‘problem solvers’. We were also curious to find out what was so complicated about his application and why couldn’t anyone else solve it?
The Problem – Water Swamped Filters In Compressed Air Lines
The customers application was for a process picking arm in a packaging company and many of these arms were employed on each section. The compressed air lines running to these machines were not run in the most ideal manner.
Initially rerouting these lines, would have been the best option, however this was ruled out because of the cost and downtime implications.
Due to the way the pipes ran, small quantities of water were able to gather in the pipes close to the machines. When they reached a certain level the water travelled down the pipe and swamped the filters already installed. This water then travelled straight to the robot arms.
This in itself would have been easy to solve for anyone; the problem came from the fact that the only available space to fit the additional filters needed was too small for any of the stock units on the market to suit the application. As is well known “size is everything! This problem was going to require a bespoke filter.
The Solution – Creating A Bespoke Additional Filtration Stage
Taking our NT1221 design we extended the multi-stage housing to take another stage so the housing started with a catchpot to take the rush of water, followed by a 7CK coalescing filter to remove the aerosol, finishing with a 5K final filter to stop particles causing any damage to the arm. The final housing was small enough yet had the capacity to handle the application.
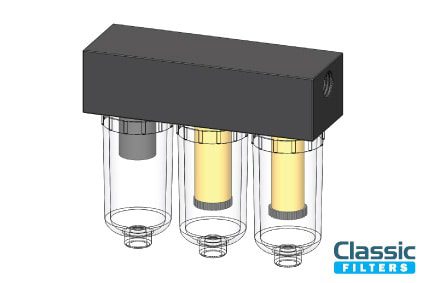
The first housing was installed as a test and after one month’s service it had already proved itself perfect for the job. The customer is happy with the multi-stage filters supplied and is gradually replacing the filters on all of its robot arms.
And the moral of this blog, remember just because its not in the catalogue doesn’t mean we can’t do it. Please do get in touch if you are looking for a cost-effective filtration solution to your problem.
Contact us by calling +44 (0)1634 724224, use the form on the right or send us an email to [email protected]